Explosion Welding Process to Obtain Clad Sheets
Introduction
MULTICLAD produces bimetallic plates also known as clad or coated plates obtained by applying the Explosive Welding Process. This work demonstrates the technical viability of the plates obtained by the above-mentioned process, which is constantly being developed in the company, with a view to saving foreign currency in the manufacture of equipment in which one of the main end users is PETROBRÁS and its contractors, as part of the effort to nationalize both raw materials and the manufacture of this equipment applied to refineries and fixed or mobile oil prospecting platforms.
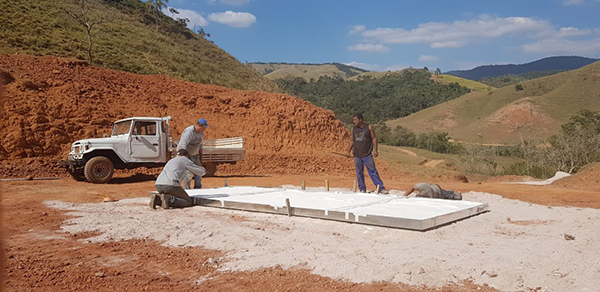
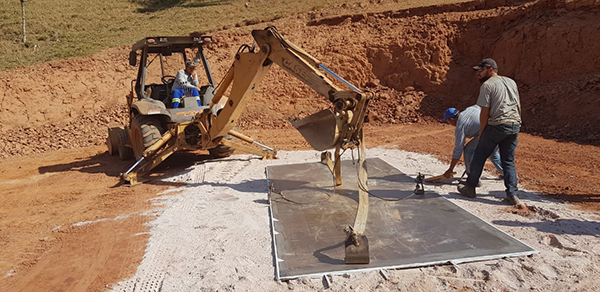
The explosion cladding process
Explosive metal welding is a solid-state welding process and the bond achieved between two metal sheets differs from fusion welding (SMAW or FCAW) in that there is no phase change at the interface. The bond produced is the result of inter-atomic forces of attraction between the atoms of the two surfaces. Explosive welding is a process of joining metal sheets in which the detonation of an explosive charge at a controlled speed transforms the detonation energy into kinetic energy applied to a sheet called the clad. This cladding plate acquires such a velocity that when it hits the base plate it transforms its kinetic energy into impact, generating pressures such that, as a result of the high shear stresses produced, the shear strength of the materials becomes negligible, the metals behaving like a low viscosity fluid that removes the oxide layers that would inhibit welding. In this impact condition, a metal jet is formed and acts between the sheets, which is the primary condition for the two materials to be joined, as can be seen in Figure 1.
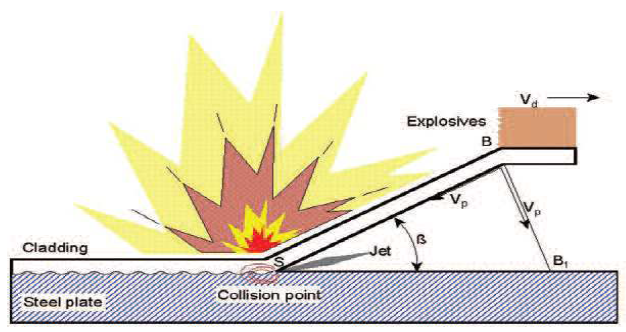
Fig. 1. Explosive welding dynamics
When all the welding parameters are properly controlled, the weld interface has the appearance of a regular wave. As well as being characteristic, the undulation gives rise to unique properties that distinguish materials obtained by explosion from other industrial processes, which do not have the quality provided by Explosive Welding. The characteristic undulation of a quality-assured weld can be seen in Figure 2.
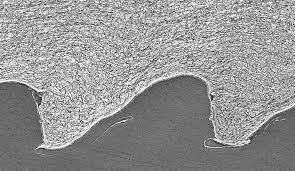
Fig. 2. Waves characteristic of the Explosive Welding Process
Applications of Clad Sheets obtained by Explosive Welding
Using explosive welding, it is possible to clad small areas up to large ones with great savings in noble materials, which are often very expensive and resistant to corrosion, as they are usually clad in carbon steel, which provides the mechanical structural strength of the equipment. In principle, the Explosive Welding process provides economic and technical viability by applying the clad plates thus obtained to the construction of equipment that would be unfeasible to manufacture by other industrial processes when analyzed in terms of cost-benefit ratio. The most important application is the production of clad plates in carbon steels coated with 300 and 400 series stainless steels, copper and copper alloys (e.g. Naval Brass), nickel and nickel alloys (e.g. Inconel, Hastelloy and Monel), Grade I and II titanium and aluminum, which have been produced by the Explosive Welding process in Brazil for over 30 years.
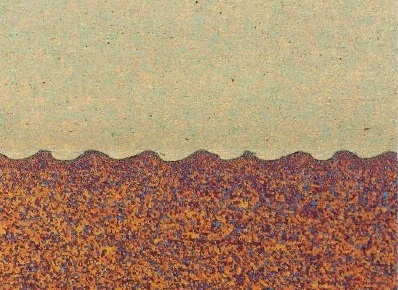
Intermetallic interface between metals clad by explosion.
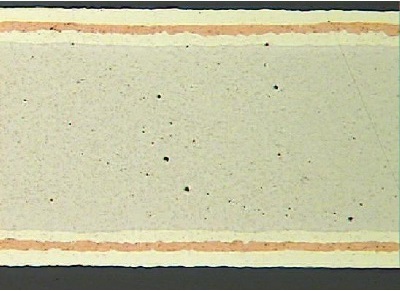
Projection of a glued profile.
Watch the video Cladding of carbon steel with naval brass for the production of equipment for the Petrobrás refinery
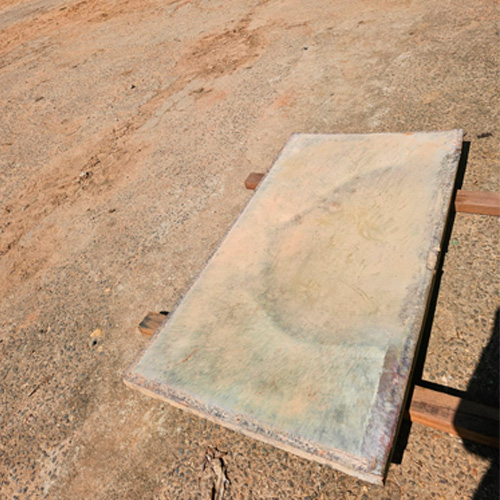
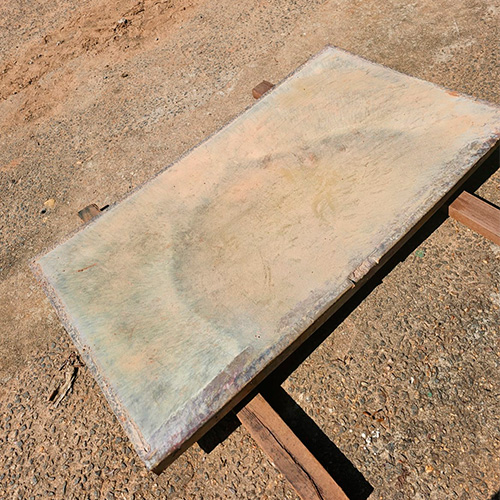
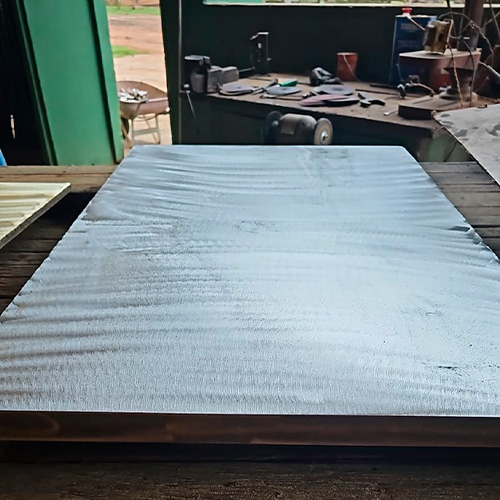
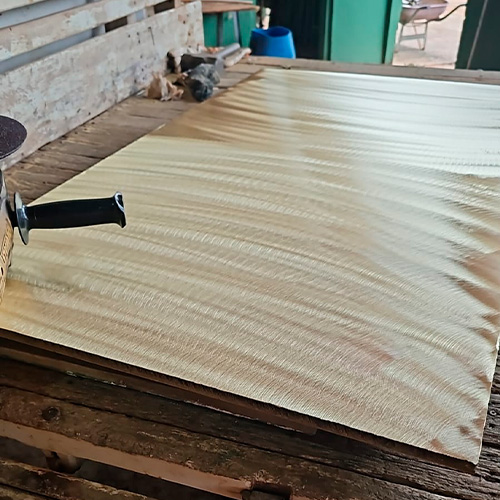
Quality of Bimetallic Sheets Clad with Explosives
Below are the results obtained from two tests carried out by MULTICLAD to qualify the weld, in which the materials were ASTM A240 Tp 316L stainless steel in thicknesses of 3.0 and 12.7 mm and ASTM A516 Grade 70 structural carbon steel. These coating thicknesses were chosen because they qualify the process for both side plates (3.0 mm) and heat exchanger mirrors (12.7 mm). The standard used to qualify the weld is ASTM A264/2003 and the destructive tests were carried out by PROAQT &lowbar Empreendimentos Tecnológicos Ltda.
ASTM A240 Tp 316L, 3.0 mm + carbon steel ASTM A516 Grade 70
In accordance with ASTM A264, tensile, bending and shear tests were carried out on welded plates measuring 500 x 500 x (3.0 + 25.4) mm.
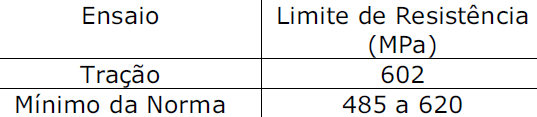
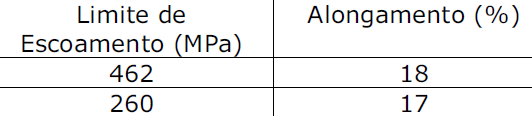
1 - Traction test
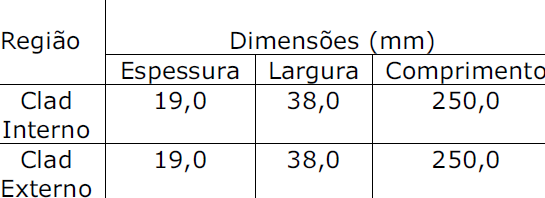
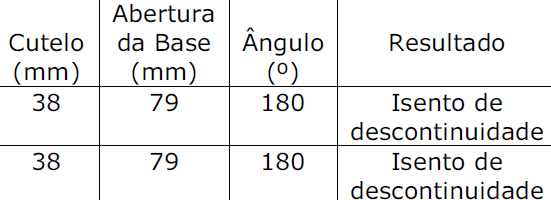
2 - Bending test

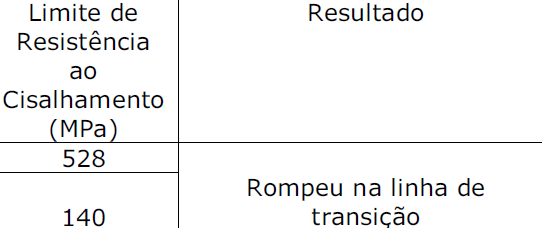
3 - Shear test
ASTM A240 Tp 316L, 12.7 mm + Carbon Steel ASTM A516 Grade 70
In accordance with ASTM A264, tensile and shear tests were carried out on welded plates measuring 500 x 500 x (12.7 + 37.5) mm.
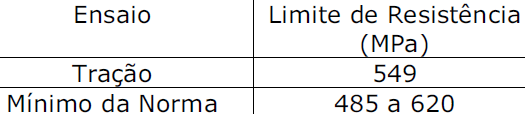
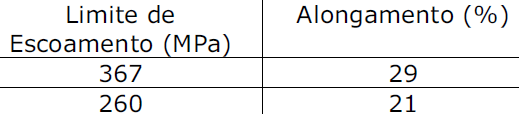
1 - Traction test
When analyzing the test results, we concluded the following:
1- The explosive welding process produces clad plates of satisfactory quality in relation to the requirements of the ASTM A264 specification;
2- The explosive welding process is qualified for both the manufacture of side plates and heat exchanger mirrors for pressure vessels;
3- The explosive welding process is qualified for clad plates with total thicknesses of less than 19 mm (< 3.2 + 15.6 mm):
3.1- In these cases, it is advisable to use 304L/316L stainless steels, which is a design condition for pressure vessels.
3.2- If it is necessary to carry out TTAT in accordance with ASME Section VIII, Div I, this heat treatment must be carried out with controlled cooling after passing the temperature of 450 °C to avoid possible sensitization. The heat treatment aims to reduce the stresses introduced by the explosion welding, restoring the ductility of the carbon steel, enabling the material to withstand the bending test as prescribed in ASTM A264.
Final considerations
As a national manufacturer of explosive welded clad plates, MULTICLAD is currently the company that has the technology for this industrial process in its entirety in Brazil, with experience in a wide variety of metal connections. In addition to the metal connections mentioned in Item III, MULTICLAD has proven experience in the explosive welding of duplex and super duplex carbon steel, among other connections. Thus, MULTICLAD is entirely at the disposal of its customers for any further studies that may contribute to enriching the fundamentals of the attractive technology of Explosive Welding, which has been implemented and used industrially in our country, with guaranteed quality.
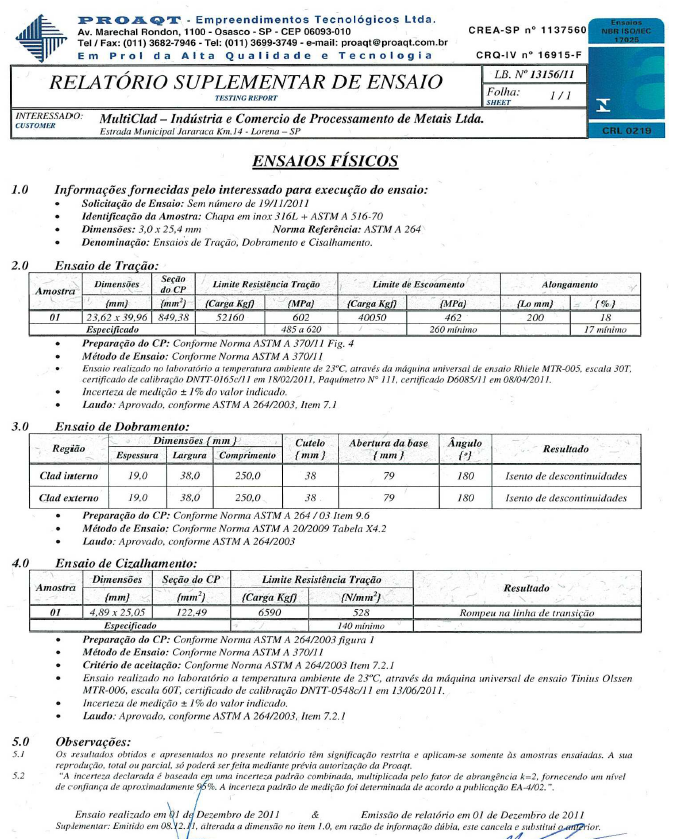
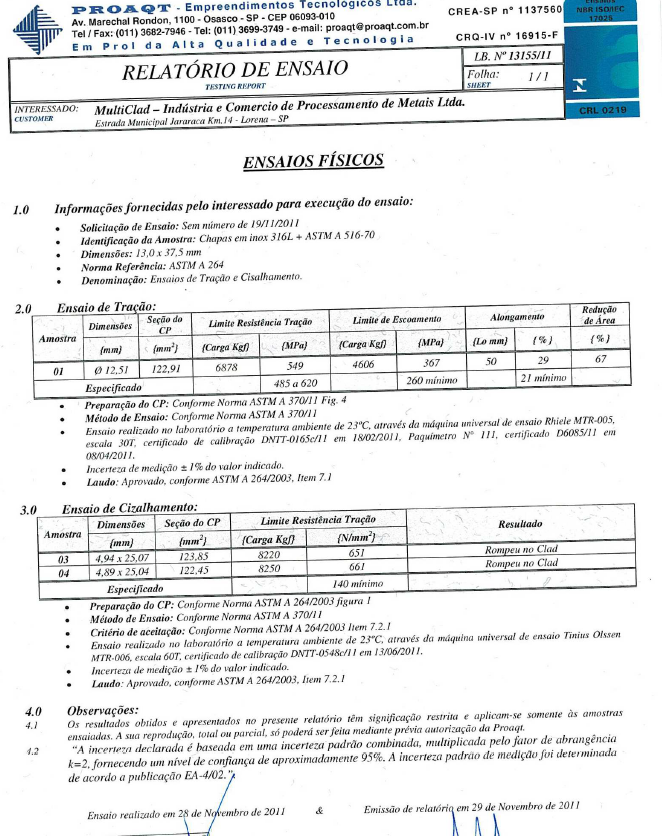
